Chief Investigators
Jarrod Leak (A2EP)
Purpose of project
The project researched the feasibility of abattoirs flexing the electrical demand of their refrigeration plants by using advanced simulations and controls with thermal storage systems, based on the success in load shedding systems at cold stores. Approximately 70% of the electricity load at an abattoir is the refrigeration plant which chills and freezes meat. There are more than 134 operational abattoirs across Australia, each with an average refrigeration load of 1.5 MWe with a total estimated electricity consumption of 1.2 TWh/year for the industry, or 0.8 TWh/year consumed in the refrigeration systems. It was hoped that this project would assist the meat industry achieve its target of being carbon neutral by 2030 and network operators with issues such as minimum demand during the middle of the day when peak solar PV production occurs.
Findings
- Load flexing opportunities identified included suction pressure modification, blast fan optimisation, thermal battery storage, electrical battery storage and hot water heat pumps
- Given the time-critical product cooling requirements, which relate to food safety standards, and very limited production flexibility, there were only limited opportunities to flex loads directly without storage
- Electric batteries offer the most significant flexible demand opportunity and are worth further investigation. Proper consideration should be given to its operation to maximise savings and maximise the battery life.
- Suction pressure modification and blast fan optimisation both provided savings with almost no capital investment (minor upgrade of controls), but only provided modest amounts of load flexing
- Thermal energy storage (TES) and hot water heat pumps offer cost savings but have substantial payback periods and thermal storage is limited to high-side (chiller) loads
- Many boning rooms have a chilled glycol loop, which could be modified to include thermal energy storage, but it is a small proportion of the total site refrigeration load and the overall economics are not attractive
- High temperature heat pumps (HTHP) operated with the existing hot water generation system could be an effective load flexing option
- Typical abattoir demand profiles would match well with solar PV generation, and HTHPs with intelligent controls would enhance this further
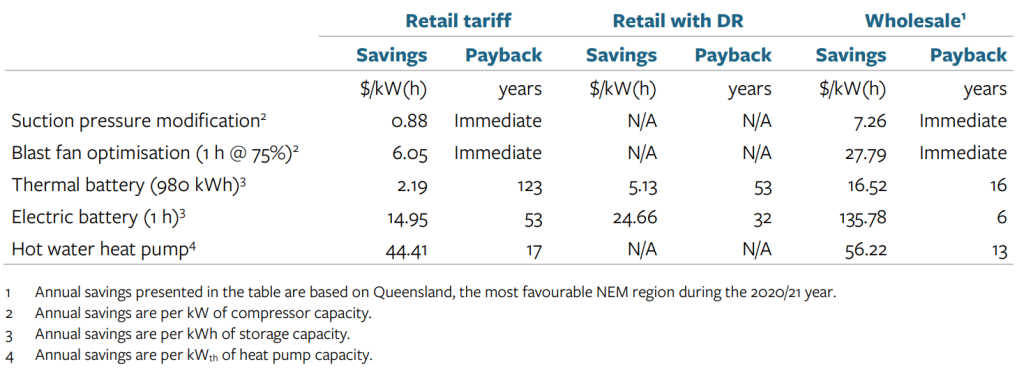
Table 1: Savings per kWh of flexible demand and simple payback periods for three pricing regimes
Potential impact
Limited potential for electricity load flexing was found in this study for abattoirs, due to the time-critical nature of the cooling process.
Research roadmap – the path to decarbonisation
Further investigation of options such as altering freezer load demand and adding cost-effective thermal storage may provide additional opportunities for this industry sector. The methods used in this study could be applied to other industrial sectors, such as food processing, which have the same less time sensitive cooling loads and greater production flexibility.
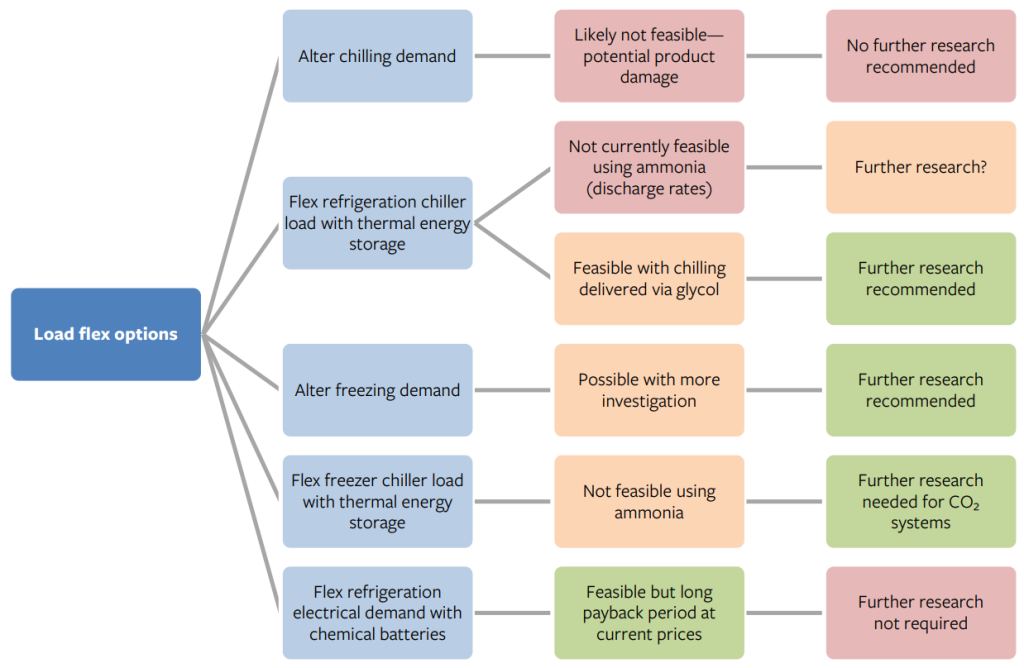
Figure 1: Abattoir load flex options and further research needs
Project partners – industry and research
Australian Alliance for Energy Productivity (A2EP) (Lead), AGL, Australian Meat Processor Corporation (AMPC), DETA Consulting, Glaciem Cooling Technologies, University of Technology Sydney (UTS)
Industry Reference Group members
C4NET, Coles, Powerlink
Published Report
Status
- Completed
Project Leaders
- Jarrod Leak, A2EP
Completion Date
August 2022
Project Code
0153